
Making a helix is little tricky task to perform with SketchUP because that program does not know helix.

Another is only rotated 180 degrees around the axis. The finished results came out pretty well but you’ll have to wait till the magazine comes out to see the results in all their glory.Double helix is two helixes with the same axis. The 3D models that had been previously generated were then assigned. For the footprint on the board, I simply added two pads. To import this into KiCAD I create a new library and then added parts for each of the wire types. As this is already negative the wire it is added rather than subtracted in the formula. The DatumPlane offset is the distance between the end of the curve and the start of the plastic. I then made the plastic sleeving length calculated from the other details. The bend radius was fixed at 1.25mm and I mirrored that onto the other end. I added a length constraint to the wire sketch and used a formula to make it multiples of 2.54mm. That allowed me to assign different materials to the wire and sleeve. When I was exporting I found that the wire came out as a single material so I first had to split the wire into 2 parts and re-do the sleeving in the new part. This allowed me to quickly export different lengths of wire without needing to make lots of adjustments. The next step after creating the basic model was to turn it into a parameterised model. That allowed me to create another sketch for the sleeve. Then after a bit of struggling, I added a datum plane to the wire and offset it by 0.5mm. But after watching a couple of tutorials I eventually produced a sketch for my wire and a path to sweep it along. My initial view of the software was that I just seemed to be clicking on things and nothing was happening. FreeCADįreeCAD is the CAD software frequently used with KiCAD and hence it does support the STEP file format required by KiCAD 3D models. But at this point I needed another option.
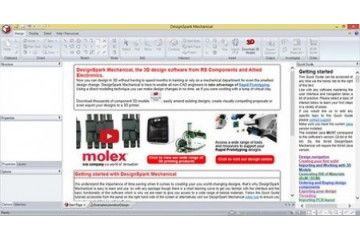
There do seem to be converter programs such as CADExchanger that will convert for example OBJ to STEP files. However, DesignSpark only supports this if you buy an exchange module for £415. Then the next step was to save the file as a “Step” file, a common interchange file format. The circuit could then be pulled/swept along the line.įinally a cylinder was added to represent the insulation. On this new plane, I drew a line up, across and back down to the second circle. To that, I added an axis through the centre of each and then a new plane based on the axis. In Design Spark Mechanical, I set the grid to 2.54mm and then I drew a couple of 1mm circles on the x-y plane. Following on from the post about designing stripboards and the one about DesignSpark, I decided to try and create some wire footprints for KiCad.
